روشهای تولید فوم گرم و فوم سرد
فومها ساختارهای سلولی هستند که توسط حبابهای گاز در طی پلیمریزاسیون پلییورتان ایجاد میشوند. فومهای انعطاف پذیر پلی یورتان (PU) مقاومت محدودی در برابر بار اعمال شده دارند، هم در هوا نفوذ کرده و هم تغییر شکل پذیر هستند. دو نوع اصلی فوم انعطاف پذیر وجود دارد، فوم گرم (hot cure) و فوم سرد (cold cure) که از نظر ترکیب و دمای فرآوری متفاوت هستند.
فوم گرم پلی اورتان به طور گستردهای مورد استفاده قرار میگیرد و ترکیب اصلی فوم واقعی را نشان میدهد، در حالی که فوم سرد پلی اورتان دارای مزایای متعددی در پردازش و خصوصیات است، به عنوان مثال، زمان قالب گیری سریعتر، خواص تحمل رطوبت بهتر و تنوع بیشتری دارند.
پردازش فوم سرد نیز به دلیل مصرف کم انرژی (دمای قالب از ۳۰ درجه تا ۶۵ درجه سانتیگراد) در مقایسه با فوم گرم (دمای قالب از ۳۰ درجه تا ۲۵۰ درجه سانتی گراد) مورد توجه است. مزیت دیگر تنوع بالای مواد نرم برای قالبهای پردازش در دمای پایین است. فوم سرد بر اساس دیفنیل متان دی ایزوسیانات (MDI) ساخته میشود در حالی که فوم گرم بر اساس تولوئن دی ایزوسیانات (TDI) است.
برای کسب اطلاعات بیشتر دربارهی ویژگی ها و همچنین تفاوت های فوم سرد و فوم گرم پلی اورتان، پیشنهاد میشود این مقاله را در وبلاگ گروه صنعتی مکرر مطالعه کنید.
روش های تولید فوم گرم و فوم سرد پلی اورتان
تهیه فومهای قالبگیریشده یک فناوری رایج است و انواع فرمولهای فوم قالبگیریشده حداقل به اندازه انواع تخته سنگها متفاوت است. مفهوم تولید فوم قالبگیری شده ساده است: اجزای فوم مخلوط شده و تزریق میشوند یا در قالب پیشساختهای که فوم هنگام تشکیل آن را پر میکند، ریخته میشود. فوم دارای زمان اقامت مشخص است و پس از مدت زمان مناسب برای اقامت در قالب برداشته میشود.
پس از برداشتن از قالب، فوم را کنار گذاشته تا پخت کامل شود. همانطور که در صنعت انجام میشود، فناوری فوم قالبگیریشده پلی اورتان از نظر تکرارپذیری پردازش و خواص بسیار بهینه شده است. بر خلاف تولید فوم تکهای، که در آن قطعات باید از یک بلوک بریده شوند، فومهای قالبدار قسمت نهایی را به عنوان بخشی از عملیات فومسازی طی میکنند.
در حالی که این روش نرخ ضایعات را کاهش میدهد و عملیات برش ساخت قطعه تمام شده را حذف میکند، توان عملیاتی یک کارخانه فوم قالبگیری کمتر است و نیاز به حضور قالبها دارد، که میتواند بسیار گران باشد. در عملیات معمول فوم قالبگیریشده، قالبها روی تجهیزات چرخشی یا بیضی شکل قرار میگیرند که به گونهای میچرخند که زمان اقامت فوم با زمان لازم برای چرخاندن و پر شدن مجدد قالب مطابقت دارد.
علاوه بر جزئیات عملیاتی، تولیدکنندگان به دلیل شکلهای پیچیدهای که سعی در ساخت آنها دارند و توانایی قالبگیری بیش از حد اجسام خاص در شکل مانند قطعات کاربردی، پوست های تزئینی یا تقویت کنندهها، ساخت فومهای قالبی را انتخاب میکنند. این ساختار به گونهای طراحی شده است که ظاهر، عملکرد و شکل صحیح را به عنوان یک قسمت ترکیبی ارائه دهد.
شکل زیر اجزای تولید فوم قالبگیری شده را از نظر جابجایی مواد اولیه و سپس پر کردن قالب نشان میدهد. قطعات واکنش پذیر ایزوسیانات (پلی ال ها، افزایندههای زنجیرهای، سورفکتانتها، کاتالیزورها، آب و غیره) در مخزن مشترک یا مخازن جداگانه خود قرار داده میشوند و سپس با ایزوسیانات در سر مخلوط کننده با انرژی بالا مخلوط میشوند. اجزای مخلوط به داخل قالب تزریق می شود، قالب بسته میشود و به اجزا اجازه میدهند پخت شوند.
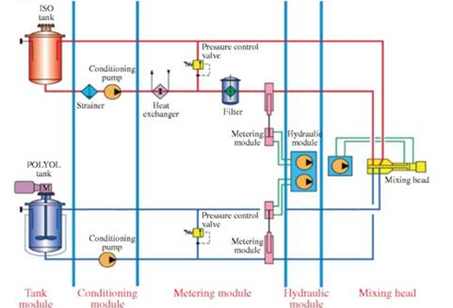
به دلیل نیاز به بهینه سازی بازدهی تولید فوم قالبگیری شده و در عین حال تولید فومهایی با دوام، راحت و متنوع، فرمولاسیون فومهای قالبگیری پیچیده است و میتواند تا حدی به عنوان یک هنر توصیف شود. سرعت قالب گیری، ریختن/تزریق و فرآیند پخت همه با فرمول انتخابی فوم کنترل میشود. به طور مشابه، جزئیات عملیات تولید میتواند تأثیر قابل توجهی بر طراحی فرمولاسیون داشته باشد. به عنوان مثال، اگر قالبهای فوم گرم شوند، میتوان از یک سیستم واکنشپذیر کمتر استفاده کرد، و اگر قالبها گرم نشده یا در دمای پایینتر گرم شوند، فرمول دیگری انتخاب میشود.
در برخی موارد، قالب تا حدی با یک فرمول پلی اورتان پر میشود تا مشخصه خاصی ایجاد شود و سپس متعاقباً با فرمولاسیون دیگری پر میشود تا ویژگیهای مورد نظر را برای بقیه قسمت تولید کند. این انعطاف پذیری عملیات فوم قالبگیری شده آن را برای تولید قطعات تخصصی بسیار مطلوب میکند، اما همچنین به پیچیدگی علم فرمول بندی کمک زیادی میکند.
همانطور که قبلاً ذکر شد، نمونههایی از فرمولهای فوم قالبگیری شده در بازتاب طیف وسیعی از گزینههای موجود، ناکافی هستند. با این حال، دستههای اصلی اجزای مورد استفاده در فومهای قالب گیری مشابه مواردی است که برای فوم سرد بلوکی استفاده میشود. اگر سازنده به طور فعال قالب خود را با عبور از یک آون داغ گرم کند، در این حالت به فوم قالب گیریشده فوم گرم میگویند.
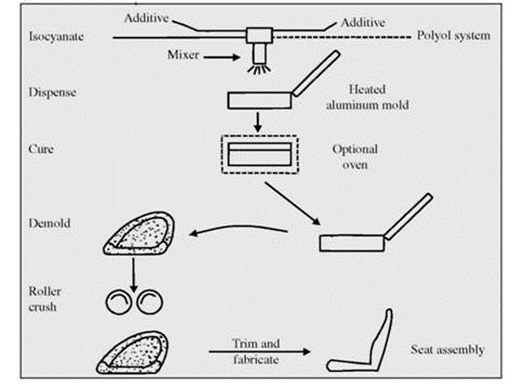
در فرمولاسیون فوم گرم از پلیالهایی استفاده میکند که ممکن است وزن مولکولی بالایی داشته باشند و در آنها یک پلی ال سه جهته توسط ایزوسیانات احاطه میشود. یک تولید کننده ممکن است از TDI، مخلوط TDI با MDI پلیمری (pDMI) استفاده کند. انتخاب بستگی به قیمت، ترجیحات سازنده و در برخی موارد جغرافیایی دارد که بر اساس قرارداد یک ایزوسیانات خاص ترجیح داده میشود.
فومهای قالبی فوم سرد پلی اورتان در تمایز با فوم گرم که قبلاً توضیح داده شد، نوآوری صنعتی جدیدی دارند و توسط قالب سردتر و با دمای آون متمایز تولید میشوند. این فومها معمولاً بیش از ۶۰ تا ۷۰ درصد انعطاف پذیری را نشان میدهند.
همانند فومهای تکهای سرد، در فوم سرد قالبی از پلی ال های با وزن مولکولی بالاتر استفاده میکنند. دمای پایین اغلب باعث میشود که فومهای قالبگیری سرد دارای تعداد بیشتری از سلولهای فوم با شبکهای دست نخورده باشند. اغلب در تولید پروتکل برای خردکردن مکانیکی فوم پس از بازیابی از قالب به منظور شکستن سلولها و افزایش جریان هوا و تنفس پذیری فوم، پروتکلهایی در دستور کار است. در حالی که در اصل میتوان به گونهای فرموله کرد که عملیات خرد کردن اضافی نباشد تا اتمام مرحله ژله شدن را تضمین کند. برخی از تولید کنندگان فوم قالبی فقط با استفاده از pMDI به عنوان ایزوسیانات، فوم را تولید میکنند.
در حقیقت انتخاب نوع ایزوسیانات، عمدتا یک موضوع ترجیحی است که عوامل مختلفی در آن نقش دارند. با این حال، چندین تفاوت در خواص فومهای تولیدی بین فومهای ساخته شده با TDI و pMDI وجود دارد. یک تفاوت این است که فومهای pMDI به طور کلی به دلیل واکنش یکنواخت عملکرد ایزوسیانات MDI سریعتر پخت میشوند (واکنش دوم ایزوسیانات در TDI معمولاً به طور قابل توجهی کندتر از اول است). در حالی که سرعت یک ویژگی ترجیحی در عملیات فوم قالب شده است، افزایش سریع ویسکوزیته میتواند با پر شدن کامل قالب تداخل داشته باشد.
با این حال، هنگامی که به طور مؤثر فرموله میشود، فوم pMDI میتواند با چرخه کوتاه تری ساخته شود. این ویژگی همچنین میتواند به تولیدکننده اجازه دهد تا دمای قالب و کوره خود را پایین بیاورد تا سینتیک شیمیایی و فرآیند را بیشتر متعادل کند. حجم مولکولی بیشتر pMDI نسبت به TDI همچنین به این معنی است که حجم قطعه سخت تولید شده برای فوم MDI بیشتر از فوم TDI است. این حجم مولکولی متفاوت منجر به این میشود که فومهای مبتنی بر MDI دارای بار بالقوه بالاتری در شاخص آب و شاخص ایزوسیانات نسبت به TDI باشند.
با این حال، ذکر شده است که فومهای قالبی با شاخص بالاتر ممکن است در برخی از خواص پویا تخریب کننده باشد در حالی که سختی بیشتری را نشان میدهند.
جنبه پیچیده فرمولاسیون فوم پلی اورتان که قبلاً به آن اشاره شد، جنبههای مرسوم استفاده از فوم قالبگیری شده است. این امر تا حد زیادی تحت تأثیر درک حدودی از راحتی است که پس از آن به سفتی فوم، انعطاف پذیری و تنفس پذیری (مربوط به جریان هوا) مربوط میشود. یکی دیگر از ویژگیهای فوم که بر اساس ترجیح منطقه ای دیکته میشود، میزان تغییر مقاومت با افزایش فشرده سازی است که گاهی اوقات عامل “پشتیبانی” یا “راحتی” نامیده میشود و به صورت کمی با نسبت سختی فوم در دو فشار متفاوت تعریف میشود.
عوامل تشکیل دهنده فوم که طراح فوم ممکن است برای مطابقت با ترجیحات مشتری آنها را مدنظر قرار دهد، عبارتند از:
- چگالی فوم (تحت تأثیر سطح آب و درصد قسمت سخت)
- ساختار سلول و باز بودن فوم (تا حدی توسط سورفکتانت و کاتالیزور دیکته میشود)
- نوع و شاخص ایزوسیانات
- عملکرد پلیال و وزن معادل
- کوپلیمر پلیال و درصد جامدات
- مواد افزودنی برای طراحی
گردآوری و ترجمه: واحد تولید محتوای گروه صنعتی مکرر
دیدگاهتان را بنویسید